By using electrical current to coat a conductive surface with a thin layer of metal, electroplating enables the modification of object properties like corrosion resistance, wear resistance, conductivity, appearance, and more. But what exactly occurs during this popular process?
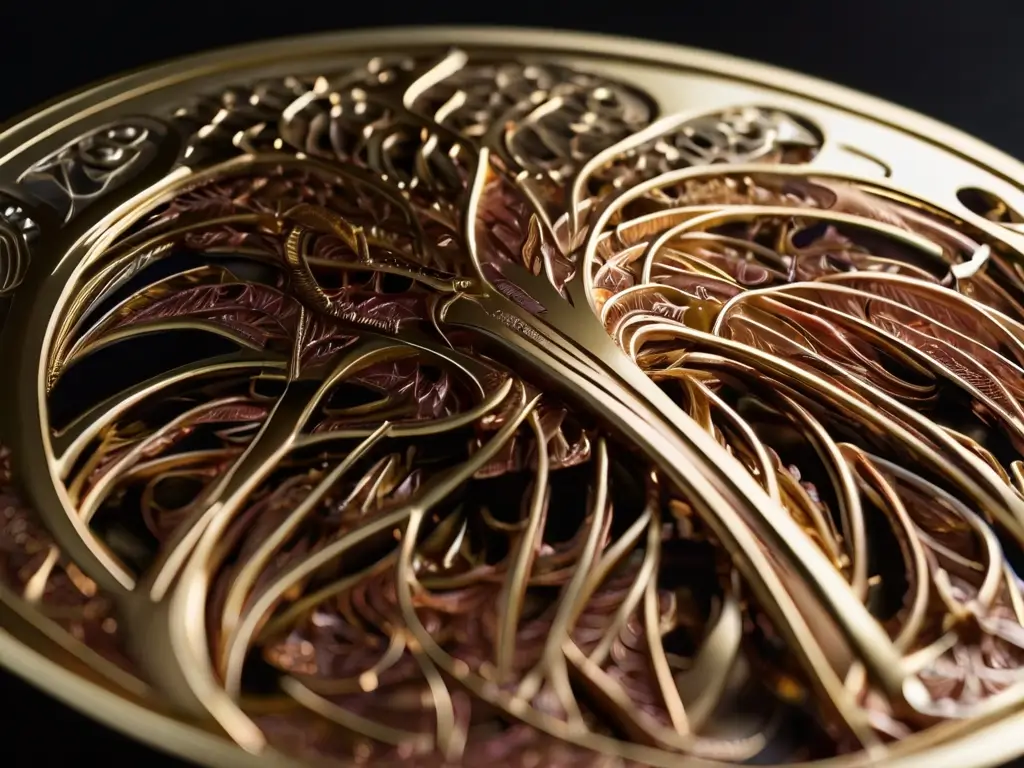
Key Takeaways
Electrodeposition: Electroplating involves the deposition of a thin layer of a material, usually a metal, onto the surface of another material using an electric current.
Redox Reaction: The process involves a redox reaction, where ions of the plating material are reduced onto the surface of the substrate, while ions from the substrate are oxidized.
Anode and Cathode: The electroplating process requires two electrodes: an anode (positive electrode) and a cathode (negative electrode). The anode is where oxidation occurs, and the cathode is where reduction occurs.
Electrolyte Solution: The electrodes are immersed in an electrolyte solution, which facilitates the flow of ions between the electrodes.
Plating Thickness: The thickness of the plating layer can be controlled by adjusting the duration of the electroplating process, the current density, and the concentration of the electrolyte solution.
Surface Preparation: The surface of the substrate must be thoroughly cleaned and prepared to ensure a strong bond between the substrate and the plating layer.
Types of Electroplating: There are several types of electroplating, including copper plating, nickel plating, chrome plating, and silver plating, each with its unique applications and benefits.
The Electroplating Process
Electroplating relies on two key actions – electrodeposition and a redox reaction.
Electrodeposition and Redox Reactions
In electroplating, electrodeposition refers to the process of depositing a thin layer of metal onto a conductive surface. This occurs due to a reduction-oxidation (redox) reaction triggered by the electric current.
Here’s a quick overview of what happens:
- The material to be plated (the anode) and the substrate to be plated (the cathode) are immersed in an electrolyte solution.
- Applying a voltage drives positively charged metal ions (cations) in the electrolyte to the cathode.
- At the cathode surface, the cations gain electrons (are reduced) and deposit onto the surface as a pure metal.
- To balance the charge, the anode simultaneously loses electrons (is oxidized) converting to its cationic form, which dissolves into the solution.
This elegant redox reaction allows metal to be stripped from the anode and deposited onto the cathode. The rate of deposition is proportional to the current, enabling precise control.
The Anode and Cathode
As outlined above, there must be two electrodes for electroplating – the anode and cathode.
The anode is positively charged and made of the plating material. As metal cations dissolve into the electrolyte, the anode disintegrates. High purity anodes enable control of deposit properties.
The cathode is negatively charged and serves as the substrate to be plated. It is usually an inert conductor like stainless steel. As cations deposit onto the cathode, they plate the substrate surface. Cathode preparation is crucial for uniform plating.
The Electrolyte Solution
The electrolyte solution facilitates ion transport between the anode and cathode while determining deposit properties. Aqueous solutions are commonly used. Organic solvents are sometimes employed when plating reactive metals.
Electrolytes contain salt forms of the plating material to provide metal ions, and other additives like buffers, brighteners, and levelers. Conductivity boosters such as acids or bases can be included. pH and concentration must be precisely controlled.
Factors Affecting Electroplating Results
Many interrelated factors influence electroplating results. Mastering control of these enables high quality, consistent plating.
Plating Thickness
Plating thickness depends on the electroplating time, current density, concentration of plating metal ions, and agitation of the electrolyte. Typical thicknesses range from microinches to mils.
Thickness uniformity requires optimizing these parameters. Too thin risks incomplete coverage, while too thick can cause embrittlement or internal stresses.
Surface Preparation
The cathode surface must be thoroughly degreased, cleaned, and etched prior to electroplating. This enhances adhesion between the substrate and deposit by removing contaminants that can cause plating flaws.
Masking precisely defines the plating area. Rack or barrel plating holds many small parts efficiently. Fixtures position and shield areas as needed.
Current Density and Concentration
Current density (amperage per cathode area) affects deposit properties like hardness and internal stress. Higher current densities increase plating speed but may reduce quality.
Electrolyte concentration impacts deposition rate and deposit qualities. Too low decreases conductivity, while too high can burn the cathode or increase brittleness.
Common Types of Electroplating
While the process fundamentals remain the same, electroplating is used to deposit many different metals for a broad range of applications.
Copper Plating
Copper electroplating provides excellent conductivity and solderability. Printed circuit boards rely on copper plating for traces and through-hole plating. Copper’s antibacterial properties also make it ideal for doorknobs, handrails, and other surfaces.
Nickel Plating
Nickel electroplating creates a smooth, lustrous finish while providing hardness and corrosion resistance. Decorative nickel plating is ubiquitous on fixtures, hardware, and automotive trim. Functional nickel plating prevents corrosion and wear on components like valves and propellers.
Chrome Plating
Chrome electroplating produces a brilliant mirrored surface that resists tarnish and abrasion. Decorative chrome is found on many household fixtures, automotive trim, and jewelry. Hard chrome plating greatly improves wear and scuff resistance on industrial components.
Silver Plating
Silver electroplating creates an eye-catching finish that protects against tarnish. It is used decoratively on cutlery, candlesticks, and jewelry. Conductive silver plating improves solderability and contact performance in electronics.
Key Applications of Electroplating
Electroplating provides indispensable functional benefits as well as aesthetic qualities across many industries.
Industrial Applications
Functional electroplating protects against wear, friction, and corrosion in the automotive, aerospace, oil and gas, textile machinery, and other demanding industrial uses. Hard chrome, nickel, and copper are common industrial platings.
Decorative Applications
Electroplating creates beautiful finishes on metal surfaces. Decorative applications include silverware, jewelry, lighting, door hardware, automotive trim pieces, and many other consumer and business products.
Electronic Applications
Printed circuit boards rely on copper and tin-lead plating for conductive traces and solderable connections. Gold plating provides corrosion-resistant, highly conductive contacts. Other specialized uses exist across electronics.
The Future of Electroplating
As a mature technology, electroplating continues to evolve and improve. Areas of focus include reducing environmental impacts, specialized alloys, nanoscale coatings, and minimizing internal stresses. The shift toward more sustainable processes and materials is driving innovation.
Automated equipment for barrel, rack, and continuous plating allow for high-volume processing with minimal labor. Tighter process controls enable precision plating for electronics and engineering challenges. Overall, electroplating will continue serving critical aesthetic, conductive, and protective roles across almost every industry imaginable.
Conclusion
Electroplating is a versatile process that relies on electric current to create metal coatings through electrodeposition and redox reactions. By understanding the anode, cathode, and electrolyte dynamics, current density, deposition variables, and surface preparation, coatings can be optimized for decorative, conductive, and functional applications. Electroplating provides beautiful finishes, enhanced conductivity, improved wear resistance, and excellent corrosion protection that are essential in everything from jewelry to aerospace. Ongoing developments will only expand electroplating’s capabilities and ubiquity moving forward.