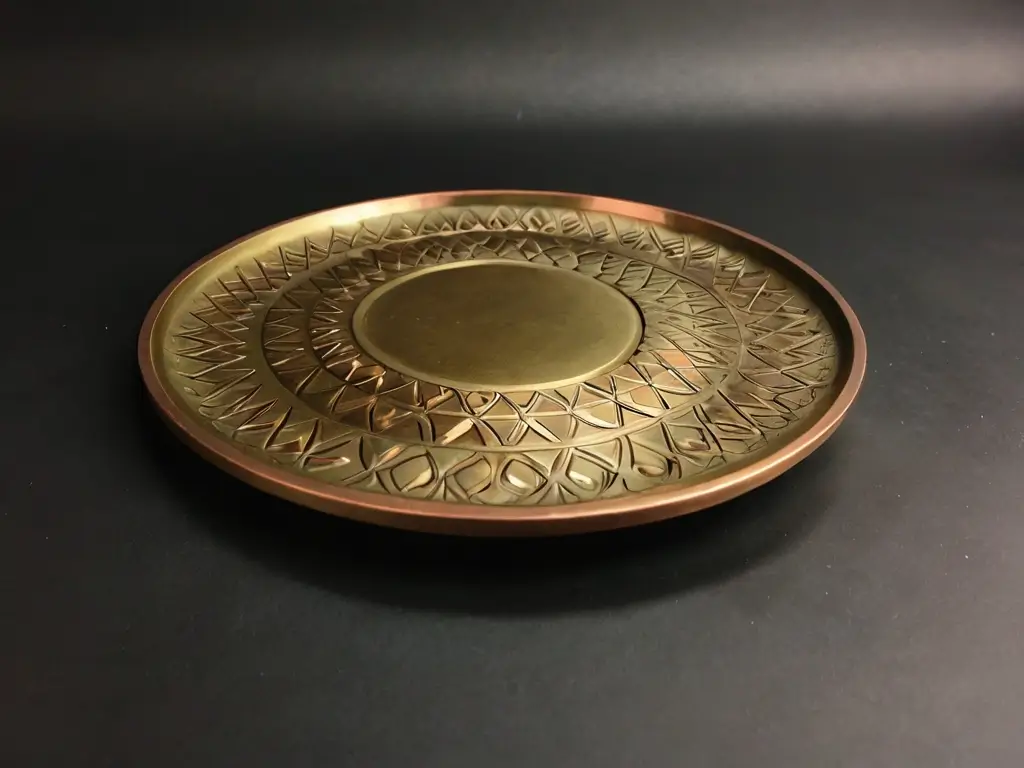
Brass is a versatile metal alloy composed of copper and zinc that is valued for its attractive golden color, durability, and corrosion resistance. While brass has many desirable properties on its own, copper plating a layer of brass can provide additional benefits like enhanced aesthetics, improved wear resistance, and better electrical conductivity.
Copper plating brass requires an understanding of the brass composition, proper surface preparation, and the technical parameters for the electroplating process. When done correctly, copper-plated brass can be an ideal material for applications ranging from decorative finishes to electronic components.
Brass as a Substrate for Copper Plating
Brass is an alloy made up of copper and zinc, with the copper content typically ranging from 55% to 95% by weight. The remaining composition is zinc, which can vary from 5% to 45%. Trace elements like lead or iron may also be present in small quantities [1].
The ratio of copper to zinc significantly impacts the properties and behavior of brass when it undergoes copper electroplating. Some key factors to consider include:
- Corrosion Resistance – Brass alloys with higher zinc content are generally more susceptible to dezincification corrosion. The zinc preferentially corrodes, leaving behind a porous copper structure [2].
- Workability – Brasses with 15-30% zinc have the best hot and cold workability. Higher zinc content tends to make the alloy more brittle [3].
- Plating Characteristics – Brasses with low zinc content (5-10%) can be readily plated with copper. High zinc brasses present challenges for copper electroplating [4].
- Mechanical Properties – Copper plating may negatively affect properties like tensile strength and hardness in brass. Ductility may increase [4].
- Appearance – Brasses with higher zinc take on a more golden color vs the reddish hue of high copper brasses [3].
Understanding the composition and temper condition of the brass is an important first step in evaluating its suitability for copper electroplating.
Pretreatment Processes for Copper Plating Brass
In order to successfully apply a copper electroplate coating, the surface of the brass must first be cleaned and prepared through a series of pretreatment steps. This serves to remove contaminants, adjust surface roughness, and activate the surface for plating.
Some common pretreatment processes used for brass prior to copper plating include:
Alkaline Cleaning
An alkaline soak helps remove oils, greases, and organic contaminants from the surface of the brass parts. Common alkaline cleaners contain ingredients like sodium hydroxide or sodium carbonate [5]. Warm temperatures around 60-70°C are typically used.
Acid Activation
After alkaline cleaning, an acid dip is frequently used to remove surface oxides and further prepare the brass surface. Sulfuric, hydrochloric, or nitric acid solutions are often used at room temperature [5]. This leaves an active metal surface ready for plating.
Electrocleaning
Electrocleaning is an electrochemical process that removes soils and oxidizes the surface in preparation for plating. It utilizes an alkaline electrolyte and an applied current density of about 30-100 A/dm2 [6].
Abrasive Blasting
For certain brass components, abrasive blasting may be used to adjust surface roughness, remove oxidation, or provide a mechanical tooth for better plating adhesion [7]. Common blasting media include aluminum oxide, glass beads, or plastic pellets.
Flux Treatment
In some cases, an acid flux may be applied just prior to copper plating to prevent re-oxidation of the activated brass surface before it enters the plating solution [4].
Choosing the appropriate pretreatment steps depends on the composition and condition of the brass substrate as well as the service environment and performance needs of the finished plated component.
The Copper Electroplating Process for Brass
The copper electroplating process itself deposit a layer of copper onto the prepared brass substrate by electrolytic means. Here are some key process details:
Plating Solution
The copper plating solution typically contains dissolved copper sulfate and sulfuric acid. Chemical additives like brighteners, levelers, and carriers may be added to refine the deposit properties [8].
Anode Material
High purity copper or phosphorized copper is commonly used as the anode material to supply the copper ions for plating. Insoluble anodes prevent contamination of the plating bath [8].
Temperature
The plating solution is maintained at a temperature between 20-30°C. Higher temperatures allow faster deposition but can reduce brightness and quality [8].
Current Density
A direct current is applied, with current densities ranging from 10-50 A/dm2. Lower densities produce smoother, finer-grained deposits [8].
Voltage
The plating voltage depends on factors like anode-cathode spacing and solution resistance. Voltages of 0.5-2V are typical for copper plating brass [9].
Agitation
Solution agitation is used to promote an even deposition across complex surfaces. Air sparging or workpiece movement can provide agitation [8].
Time
Depending on the desired thickness, plating duration may range from minutes to hours. Plating rate is about 10-25 μm per hour at high current densities [8].
Controlling these parameters allows the electroplating process to be tailored to achieve the required copper coating thickness, appearance, and properties.
Post-Plating Processes
After copper electroplating, further steps help finalize the plated brass components:
- Rinsing – The parts are thoroughly rinsed in water to remove plating solution dragout. Deionized water provides final cleanliness.
- Drying – Gentle air or oven drying prevents water spotting. Excessive heat can anneal the copper deposit, altering its properties [10].
- Stripping – Masking materials or racks are chemically stripped away after plating is complete. This exposes the full plated surface.
- Brushing – Light brushing with a nylon or brass brush evens out surface roughness and enhances reflectivity [10].
- Lacquering – A clear protective lacquer may be applied to prevent tarnishing of the freshly plated copper surface [10].
Proper post-plate handling ensures the copper plated brass finish retains its intended appearance and properties in actual service.
Applications and Benefits of Copper Plated Brass
Copper electroplating is done onto brass for both decorative and functional reasons across a diverse array of end use applications:
- Electrical components – Copper plating improves conductivity, allowing brass connectors, pins, and lead wires to have reduced contact resistance.
- Marine fittings – The corrosion protection provided by a copper plating helps brass fittings better withstand seawater exposure.
- Musical instruments – Plating provides an attractive finish for brass instrument parts and helps prevent tarnish.
- Ammunition casings – Copper coated casings have improved feeding and extraction performance and aesthetics.
- Decorative hardware – Doorknobs, light fixtures, and other brass hardware items attain an appealing copper finish.
Key benefits of copper plated brass include:
- Enhanced surface appearance and reflectivity
- Improved wear life and scratch/abrasion resistance
- Increased hardness and durability
- Better electrical and thermal conductivity
- Reduced tarnishing and corrosion protection
- Easier soldering and brazing
By providing both visual and functional upgrades, copper plating expands the utility of brass components across many demanding applications.
Challenges and Limitations of Copper Plating Brass
While copper plating offers some clear advantages, the process also comes with some inherent challenges and limitations:
- Plating adhesion – High zinc brasses allow only minimal copper deposition before adhesion loss occurs. Pretreatment is essential.
- Hydrogen embrittlement – Absorbed hydrogen during plating can make brass brittle and prone to cracking. Careful process control is needed.
- Stress generation – Internal stresses from electrodeposition can distort parts or initiate cracking in the brass substrate.
- Thickness limitations – Standard plating processes allow only thin copper coatings up to about 25-50 microns to be applied to brass.
- Cost – The multiple process steps required make copper plating relatively expensive compared to alternative surface treatments.
By understanding these potential pitfalls, processors can take steps to mitigate issues through proper brass selection, surface preparation, and process control.
Best Practices for Copper Plating Brass
To achieve high quality, consistent results from copper plating, processors should follow these best practice guidelines:
- Analyze substrate – Check brass composition and properties to ensure compatibility with plating process.
- Clean thoroughly – Use alkaline and acid baths to remove all oils, oxides, and soils from brass surface.
- Activate fully – Employ acid dips, anodic etching, or abrasive blasting to properly activate the surface.
- Pre-plate dip – Use a flux or pre-dip to prevent re-oxidation of activated surfaces before plating.
- Monitor plating solution – Frequently test solution chemistry and additive concentrations to keep bath optimized.
- Control current density – Use proper current levels to achieve desired plating rate and deposit qualities.
- Use air agitation – Keep solution well-agitated near parts to provide an even, high quality deposit.
- Rinse completely – Rinse parts thoroughly after plating to remove all solution dragout.
By carefully following these guidelines, processors can achieve repeatable, high-quality copper plated brass components tailored to the needs of specific applications.
Conclusion
The technique of copper electroplating brass provides an excellent means for enhancing the surface properties of brass components while retaining the many intrinsic benefits of the underlying brass alloy.
With proper plating bath chemistry, surface preparation, and process control, functional copper plate coatings can be deposited on a range of brass alloys. The result is a versatile plated material with improved conductivity, corrosion resistance, wear properties, and aesthetic qualities.
While certain challenges exist, the expanding use of copper plated brass across diverse industries demonstrates the value of this plating process when applied appropriately. By gaining a full understanding of the deposition mechanisms, processors can selectively employ copper electroplating to harness the combined characteristics of brass and copper in one high-performance material.
References
[1] ASM Handbook, Vol 5: Surface Engineering. “Electroplated Coatings.” p 29-30.
[2] Kear G., Barker B.D., Walsh F.C. “Electrochemical corrosion of unalloyed copper in chloride media––a critical review.” Corrosion Science. Vol 46, Issue 1, 2004. p 109-135.
[3] “Brass and Bronze Standard Casting Alloys.” United States Brass & Copper. http://www.usbronzecasting.com/alloys
[4] Lowenheim F. A. “Electroplating”. McGraw-Hill, 1978. p 446-448.
[5] Paunovic M., Schlesinger M. “Fundamentals of Electrochemical Deposition”. John Wiley & Sons, 2006. p 136-137.
[6] Suraski D., Seamans G. “Fundamentals of Electroplating and Electroforming”. 4th Edition, Galvotec Alloys, Inc, 2000.
[7] Spiro A. “Getting Good Adhesion on Hard-to-Plate Substrates”. Products Finishing Magazine. June 2013.
[8] Safranek W. H. “The Properties of Electrodeposited Metals and Alloys”. Amer Electroplaters and Surface Finishers Society, 1986. p 243-285.
[9] Graves P.R. “Copper Plating”. Metal Finishing Magazine, Vol 93, 1995. p 355-361.
[10] Lowenheim F. A. “Modern Electroplating”. 3rd Edition, John Wiley & Sons, 1974. p 201-205.