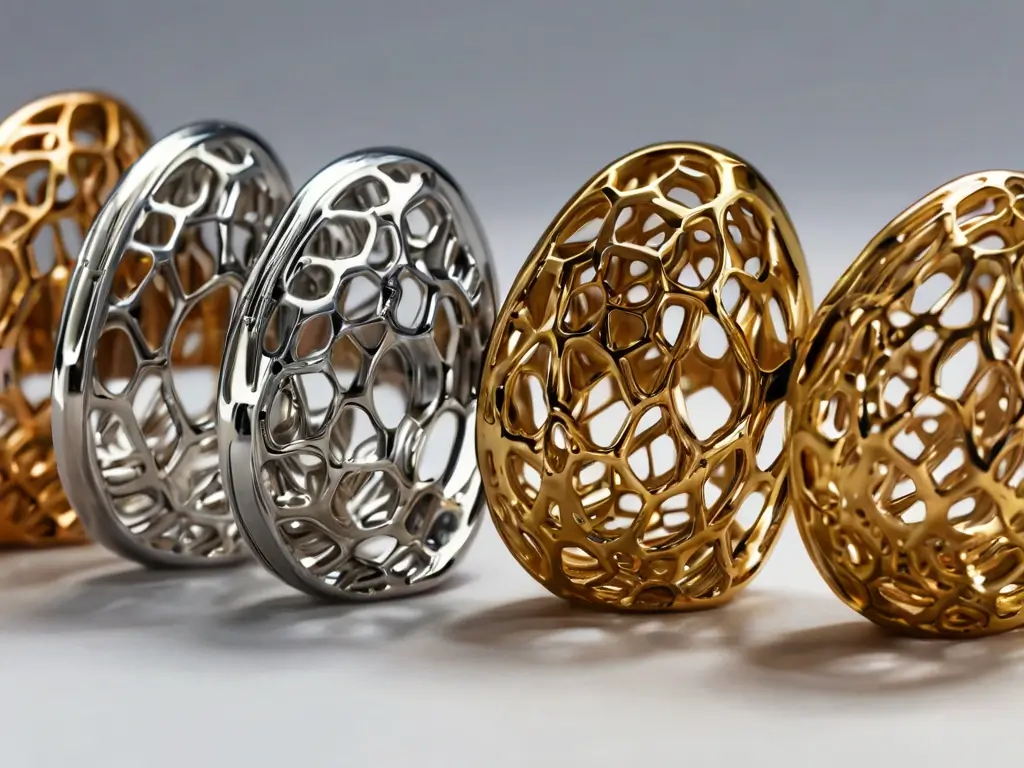
Electroplating is a technique that can transform the look and feel of 3D printed objects by coating them with a metallic layer. This process involves passing an electric current through a solution containing metal ions, causing the ions to deposit onto the surface of the 3D printed part and form a metal coating.
Electroplating 3D prints opens up new possibilities for both decorative and functional applications. Aesthetically, it provides a realistic metallic appearance, adding a shiny, chrome-like finish. Functionally, the added metal layer improves strength, durability, and wear resistance.
However, electroplating 3D prints also comes with challenges. The process requires an understanding of the chemistry involved and some trial and error to achieve high-quality results.
The Electroplating Process Step-by-Step
Electroplating may seem complex, but it involves just a few key steps. Here is a breakdown of the electroplating process from start to finish:
Step 1: Design and Print the Part
- The design of the part will impact the electroplating process and results. Optimal designs have:
- Smooth surfaces and edges
- No small details or holes
- Open access to all surfaces needing plating
- FDM prints can be used but have a rough surface. Smoothing techniques help.
- SLA resin prints provide the best starting surface.
Step 2: Clean and Prepare the Surface
- Thoroughly clean the part to remove any oil, grease, or residue. Dish soap and isopropyl alcohol work well.
- For FDM prints, sanding, priming, and filling helps smooth the layered surface.
- Apply conductive paint or carbon spray to make the surface conductive.
Step 3: Set Up the Electroplating Bath
- Fill a non-conductive tank with electroplating solution (electrolyte).
- Obtain a metal anode matching the type of metal being plated (nickel, copper, etc.).
- Connect the anode and cathode (3D printed part) to a power source.
Step 4: Electroplate the Part
- Immerse the part in the electrolyte, ensuring full contact with the anode.
- Turn on the power and electroplate for the desired duration, monitoring the progress.
- Time required ranges from 30 minutes to several hours depending on factors like current density.
Step 5: Rinse and Dry the Part
- Remove the electroplated part from the bath and rinse thoroughly with water.
- Allow the part to fully dry. At this point, it will have a metallic coating matching the anode metal.
Equipment Needed
Electroplating at home is totally feasible with relatively inexpensive and accessible equipment:
- Power Supply – Provides direct current. Can use a battery charger, DC power supply, or solar panel.
- Conductive Paint or Carbon Spray – Applied to the 3D print before plating. Improves conductivity.
- Non-Conductive Tank – Holds the electroplating solution. Glass or plastic work well.
- Anode – The source of the metal ions. Obtained as metal rods, sheets, baskets, or nuggets.
- Alligator Clips – Connect anode and cathode to power supply. Insulated types recommended.
- Personal Protective Equipment – Gloves, goggles, mask when handling chemicals.
Optional items include stirrers or bubblers to agitate the solution and improve results.
Electroplating Solutions
The electrolyte solution provides the metal ions for plating onto the part surface. Common options include:
- Nickel Sulfamate – For a shiny nickel finish.
- Copper Sulfate – For a copper appearance.
- Gold Potassium Cyanide – For gold plating. More complex and dangerous.
- Tin-Bismuth – For a matte tin-white look.
These chemicals can be purchased from online vendors in premade solutions. Follow all safety precautions when handling.
Plating Different 3D Printing Processes
The 3D printing process used to create the part affects the electroplating process and results. Here is a comparison:
- FDM – The layered surface causes adhesion issues. Must be sanded and primed for plating.
- SLA – The smooth resin surface allows for direct plating with good adhesion.
- SLS – Difficult. Porosity causes solution seepage. Special sealing required.
- MJF – Easy to plate. Provides smooth parts with good detail.
FDM requires more preparation but can be electroplated with proper processing. SLA is ideal. SLS is challenging and may not achieve quality plating.
Step-by-Step Process for FDM Prints
Since FDM is a common 3D printing process, here are the detailed steps for prepping these prints:
- Sand the print with progressively finer grit sandpaper.
- Fill any gaps or grooves with filler primer.
- Apply 1-2 coats of high-fill primer to smooth the surface.
- Wet sand again with fine grit paper.
- Clean thoroughly with soap and water.
- Apply conductive paint. Allow to dry fully.
- Electroplate as normal, starting with lower current density.
This smoothing process helps the plated metal adhere properly to the FDM print.
Electroplating Technique and Results
The electroplating technique impacts the quality of the metal finish. Follow these tips:
- Maintain proper current density – Too high causes burning and pitting. Too low slows plating.
- Use distilled water for rinsing. Impurities can stain the finish.
- Agitate the solution using a stirrer or bubbler for even coverage.
- Wear rubber gloves to avoid hand oils transferring to the part.
- Adjust time to control coating thickness. Thin coats take 10-60 minutes.
With practice, electroplated 3D prints can achieve results resembling chrome-plated plastic or metal objects. The coating will be thin so the underlying print surface still influences the look.
Common Challenges and Solutions
Electroplating 3D prints brings unique challenges. Here are some common issues and troubleshooting tips:
Problem: Uneven plating or bare spots
Solution: Ensure part has conductive coating before plating. Agitate solution. Adjust position of part.
Problem: Plating burns or pits the surface
Solution: Reduce current density. Use pulsed power supply. Check for shorts.
Problem: Plating is too thin or will not coat
Solution: Increase plating time. Check electrolyte concentration and pH.
Problem: Plating flakes off
Solution: Roughen surface and use primer for better adhesion on FDM prints.
Problem: Dull, grainy or poor finish
Solution: Filter and replace electrolyte. Check current density. Improve part prep.
Safety Precautions
Electroplating involves hazardous chemicals. Take these safety steps:
- Wear gloves, goggles, and a mask when mixing solutions and handling chemicals.
- Work in a well-ventilated area to prevent buildup of chemical fumes.
- Never eat or drink near the electroplating setup.
- Store solutions securely in spill-proof containers.
- Follow all chemical safety warnings and dispose of waste properly.
- Unplug power supply before accessing the plating bath.
Exercise caution when electroplating to avoid chemical burns or exposure. Have an emergency eyewash station nearby in case of splashes.
Functional Applications of Electroplated 3D Prints
Beyond aesthetics, electroplating can enhance 3D prints for functional uses:
- Wear resistance – Protects against friction and abrasion. Useful for bearings, gears, sliders.
- Corrosion protection – The plated layer resists oxidation and chemical damage.
- Improved strength – Reinforces against breakage and cracking.
- Conductivity – Allows use as electrodes, contacts, and wiring.
- Reflectivity – Can create reflective chrome-like finishes.
Electroplating opens new opportunities for strong, durable 3D printed parts.
Achieving Different Metal Finishes
By selecting the appropriate anode metal and electroplating solution, a variety of metal finishes can be achieved:
- Nickel – Shiny silver finish. Most common.
- Copper – Warm reddish finish.
- Tin – Silvery white finish. Provides corrosion resistance.
- Brass – Gold-toned finish. Combines copper and zinc.
- Gold – Expensive but provides a luxurious finish.
- Silver – Bright and reflective finish.
- Chromium – Mirror-like chrome finish possible. More complex process.
The metal finish not only changes the appearance but also impacts the properties imparted to the 3D printed part.
Industrial vs. DIY Electroplating
Electroplating is done both on an industrial scale and by hobbyists:
Industrial Electroplating
- Uses automated equipment for high volume production.
- Strict process controls for consistency.
- Hazardous waste disposal regulations.
- Can plate full metal coatings not just thin layers.
- Limited metal options.
DIY Electroplating
- Manual small-scale setups.
- Experimentation and customization possible.
- Can only achieve thin decorative plating.
- More flexibility in parts and metals.
- Affordable way to try out process.
Each approach has tradeoffs. Industrial plating emphasizes efficiency and quality, while DIY focuses more on customization and variety.
Future Potential of Electroplated 3D Printing
Advancements in materials and processes are expanding the possibilities of electroplated 3D printing:
- Hybrid printing – Combining electroplated plastic with metal 3D printing allows complex geometries and embedded conductive traces.
- Selective plating – Using masks or applied currents enables plating only specific regions of a print.
- Nanoscale plating – Electroless processes can deposit metal layers atom-by-atom for precision electronics.
- Functional gradients – Varying plating thickness or materials across a part creates graded properties.
- Plated composites – Coatings enhance strength, conductivity, friction properties, etc. of composites.
As technology improves, electroplating will become an even more valuable tool for enhancing 3D printed parts.
Conclusion
Electroplating brings 3D printed objects to the next level with visually stunning metallic finishes and improved physical properties. Although a complex process requiring care and precision, spectacular results are possible with the right techniques. This guide covers all the key steps involved in electroplating 3D prints at home, enabling your own experiments with this transformative post-processing method. Mastering electroplating opens new opportunities to create professional quality custom 3D printed parts.