Electropolishing is an innovative metal finishing process that produces a smooth, bright surface on metal parts and products. This high-tech electrochemical technique offers numerous benefits over traditional mechanical polishing methods.
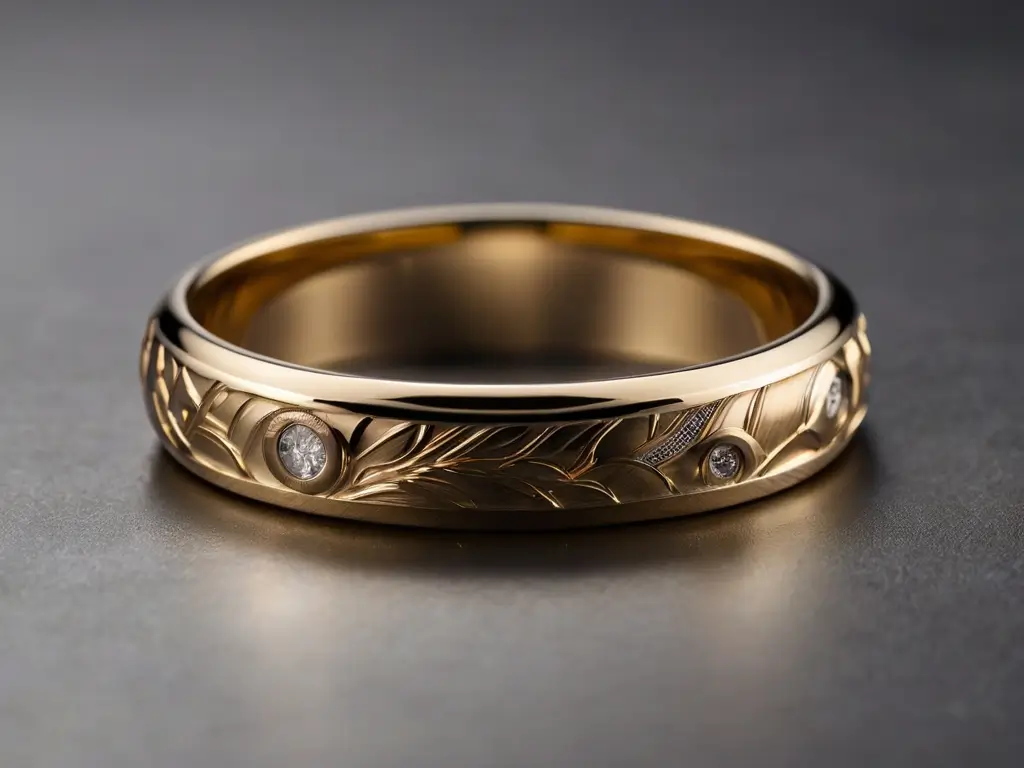
In recent years, electropolishing has become an increasingly popular option across various industries including medical devices, aerospace, and semiconductors. The ability to achieve precise, consistent results on intricate geometries makes it an ideal choice for today’s highly engineered components.
What is Electropolishing?
Electropolishing, often referred to as “reverse electroplating,” is an electrochemical process used to produce a smooth, mirror-like finish on metal surfaces. It involves placing the metal workpiece to be polished as the anode (positive electrode) into a bath containing a concentrated electrolyte solution.
When direct current is applied, it causes the anodic metal surface to dissolve into the electrolyte. This results in a controlled, layer-by-layer removal of microscopic peaks and surface irregularities. The outcome is a remarkably smooth, reflective surface with enhanced properties.
Unlike mechanical polishing techniques that grind down surfaces through abrasion, electropolishing achieves its results through a non-contact, chemical process. This makes it well-suited for working with delicate parts and complex geometries that may be difficult to polish using conventional methods.
How Does Electropolishing Work?
The electropolishing process relies on an electrolytic cell consisting of the metal workpiece serving as the anode, the electrolyte solution, and the cathode. The workpiece is submerged into the electrolyte bath and connected to the positive terminal of the power supply, making it the anode.
When voltage is applied, it creates a controlled electrochemical reaction causing the anodic metal surface to slowly dissolve into the electrolyte. This electrochemical dissolution is key to how electropolishing works.
Due to differences in current density across the surface, the peaks and microscopic irregularities on the metal dissolve faster than the valleys and depressions. Over time, this results in a gradual leveling or “planarization” as the peaks are preferentially removed at a higher rate than the lower areas.
The end result is a remarkably smooth surface at the sub-micron level. When done properly, electropolishing can produce surfaces with average roughness (Ra) values below 0.1 microns. For comparison, a typical mechanically polished surface may have an Ra between 0.3-0.8 microns.
The electrolyte solution is also critical for controlling the reactions and removal rate. It typically consists of a concentrated acid mixture designed to rapidly dissolve the metal surface under the influence of electrical current. Phosphoric, sulfuric, perchloric, and chromic acid baths are commonly used.
Benefits of Electropolishing
Compared to mechanical polishing techniques, electropolishing offers some unique advantages that make it an appealing finishing option:
Improved Surface Finish
The primary benefit of electropolishing is its ability to produce a remarkably smooth, bright surface finish. The electrochemical reactions allow it to level microscopic peaks and valleys for a consistent, uniform appearance not easily achievable through grinding or buffing.
Parts and products finished with electropolishing often have a chrome-like, highly reflective surface quality. This lustrous, “mirror finish” also enhances the visual appeal of metal surfaces.
Enhanced Corrosion Resistance
The removal of surface impurities and microscopic irregularities helps improve corrosion resistance. Electropolishing eliminates micro-crevices that can trap corrosive agents. The resulting smooth surface with increased passivity allows for easier cleaning as well.
For applications where corrosion resistance is critical, electropolishing provides an added level of protection compared to standard mechanical finishing alone.
Deburring Capabilities
In addition to polishing, electropolishing also serves as an effective deburring process. The electrochemical reactions can dissolve away unwanted burrs or sharp edges from machined parts, slots, holes, and other difficult to reach internal surfaces.
The ability to deburr and finish complex geometries in one step makes electropolishing an appealing option over separate mechanical deburring and polishing operations.
Microscopic Applications
Due to its precision and control, electropolishing can produce the ultra-smooth finishes needed for microscopic devices and components. This makes it ideal for polishing delicate parts used in scientific instruments and other leading-edge technologies.
The process allows small, intricate pieces to be polished without damage or distortion to their precise dimensions and shapes. Parts with slotted tubes, tiny holes, and complex internal channels can be effectively finished by electropolishing.
Applications of Electropolishing
Thanks to its unique benefits and capabilities, electropolishing is utilized across a diverse range of industries and applications:
Medical Devices
Polishing surgical instruments, implants, and other medical devices to an ultra-smooth finish is critical for biocompatibility and corrosion resistance. Electropolishing provides the level of precision and cleanliness needed for medical applications. Guidewires, needles, forceps, scalpels, stents, and orthopedic implants are some examples where electropolishing enhances performance and safety.
Aerospace and Semiconductors
These high-tech industries rely on advanced materials and components engineered to tight tolerances. Electropolishing creates the pristine, ultra-smooth finishes needed for aerospace engine components and high-purity semiconductor fabrication parts operating in extreme environments.
Scientific Research
Electropolishing is used to prepare extremely smooth metal samples for electron microscopy. The process reveals intricate metallurgical microstructures needed for detailed analysis and research. It also provides precision polishing of delicate instrument components like apertures, collimators, and casings used in various scientific fields.
Jewelry and Metal Finishing
For precious metals like gold and silver, electropolishing can produce brilliant, mirror-like surfaces that enhance the aesthetic beauty of jewelry. It also offers an alternative to the chemical and abrasive processes traditionally used in metal finishing for achieving luster on various alloys.
Key Considerations for Electropolishing
While electropolishing has many advantages, there are some key factors to consider when determining if it’s the right surface finishing solution:
- Part Geometry – The process works best on simple, open geometries. Very complex shapes may require special fixturing and cathode placements to distribute current density evenly across all surfaces. Internal passages must allow for electrolyte flow-through.
- Metallurgy – Electropolishing works on many alloys like stainless steel, aluminum, copper, titanium, tantalum, platinum, and nickel. However, each metal has specific parameters and electrolyte solutions.
- Surface Condition – For best results, parts should have a clean, smooth surface from machining or other pre-finishing before electropolishing. Extremely rough surfaces may need additional steps.
- Cost – Electropolishing has higher equipment costs compared to basic mechanical polishing. Production line setups maximize throughput and cost-efficiency. Smaller batches may be better suited for toll processing by a specialty shop.
- Safety – The process uses strong acids and direct electrical currents. Proper training and protective equipment are required to work safely with electropolishing equipment.
Conclusion
Electropolishing provides a high-precision finishing method to improve surface properties and achieve a mirror-like metal surface. The electrochemical process levels microscopic peaks and valleys in a controlled manner not easily replicable by mechanical polishing techniques.
Key benefits like enhanced corrosion resistance, deburring abilities, and ultra-smooth finishes make it an important finishing option across medical, aerospace, semiconductor, and other leading-edge industries.