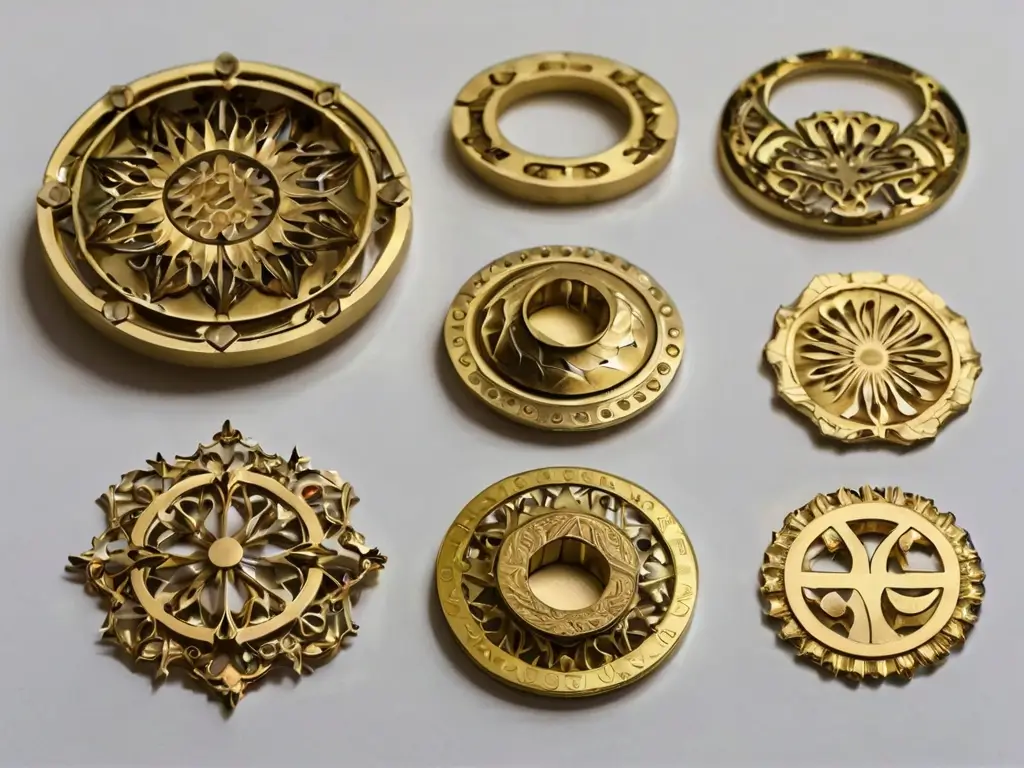
Brass plating is a versatile metal finishing process used to apply a layer of brass onto parts and components made of other metals. The brass coating imparts an attractive golden color while also providing excellent corrosion resistance, wear resistance, and solderability. Brass plated parts are commonly found in plumbing fittings, electrical hardware, automotive trim pieces, musical instruments, jewelry, and decorative metalwork.
Surface Preparation Prior to Plating
Achieving flawless brass plating requires an impeccably clean substrate free of oils, scale, oxides and other contaminants. Any foreign material can lead to poor adhesion or defects in the plated layer. Proper surface prep clears the way for the brass to deposit evenly across every surface.
Degreasing
The first step is degreasing to remove all traces of oils, grease, wax, polish residues, and other organic contaminants from the surface. Parts are fully submerged in heated alkaline or emulsion-type degreasing solutions. Common degreasing agents include sodium hydroxide, potassium hydroxide, surfactants, and detergents.
As the degreaser solution dissolves and lifts away greasy soils, parts should be continuously agitated for 5-10 minutes to expose all surfaces. Options for agitation include pump circulation, compressed air bubbling, or rotating baskets. Proper dwell times and temperatures must be observed based on the degreaser’s specifications.
Thorough degreasing is critical prior to any metal finishing process. Oils left on the surface will contaminate plating solutions and prevent solutions from reaching the substrate. This results in skipped plating and poor adhesion. Degreasing is mandatory even for new parts right out of machining since cutting fluids leave oily residues.
Rinsing After Degreasing
Once degreasing is complete, parts must be thoroughly rinsed to remove all traces of cleaning agents. Failure to properly rinse off degreasers will lead to foaming and contamination issues in subsequent process steps.
Rinsing is performed by immersing parts in a series of overflowing cold water rinse tanks. Fresh water continually displaces contaminated water to prevent redeposition of soils back onto the parts. A minimum 3-stage rinse is recommended for most degreasing applications. Rinse water may be filtered and recycled to reduce waste.
Pickling
After rinsing away degreaser residues, parts undergo pickling in a heated sulfuric or hydrochloric acid solution to remove surface oxides and scale. The acid reacts with metallic oxides and corrodes them away, leaving a pristine bare metal surface.
Pickling baths typically consist of 10-30% sulfuric acid by volume heated to 140-212°F. Parts are immersed for 2-5 minutes with proper agitation until all oxides visibly disappear. Hydrochloric acid can also be used alone or blended with sulfuric acid. Other pickling inhibitors may be added to prevent over-etching.
Pickling thoroughly cleans off rust, smut, heat scale, tarnish films, annealing oxides, and other oxidative contaminants down to shiny bare metal. It removes the passivated outer layer and activates the surface for subsequent plating steps.
Post-Pickling Rinse
Following pickling, residual acid must be completely rinsed off to prevent acid carryover into plating solutions. Rinsing is performed using a series of cold water rinse tanks with sufficient agitation and overflow.
A minimum 5-stage rinse is recommended after pickling, with the first tank agitated and heated to 120-140°F to accelerate removal of acid residues. The final rinse water should test below 20ppm total dissolved solids for most plating processes.
Thorough rinsing is crucial to prevent acid dragout, which can destabilize plating baths, cause pitting, and interfere with adhesion. No acids should remain on the surface before plating.
Surface Activation
The final surface prep step is activation in an acid dip designed to etch the substrate and improve plating adhesion. Parts are dipped in a 5-20% solution of hydrochloric, sulfuric, or phosphoric acid for 30-90 seconds prior to plating.
Activation removes any residual surface oxides and provides microroughness for the plating to mechanically key into. It leaves a chemically clean and wettable surface optimized for nucleation of the plated deposit.
After activation, parts may go through a quick rinse or directly into the plating bath while still wet. The activated surface must not be allowed to dry or oxidize prior to plating.
Brass Plating Process
With pristine surface prep complete, parts are ready for the brass plating process itself. Brass electroplating involves submerging parts in a heated plating solution containing brass metal ions and applying electrical current to deposit the brass coating.
Strike Plating – Copper or Nickel
Before immersing in the main brass plating bath, parts typically receive an initial strike layer of copper or nickel. Strike plating provides a conductive base layer that allows the subsequent brass deposit to nucleate and build up more evenly.
For copper strike, parts are dipped in 20-40 g/L copper cyanide solution with a current density around 40 A/ft2. Copper strike should be 0.0001-0.0004 inches thick. Nickel strike uses a 10-20 g/L nickel chloride or sulfate bath.
Strike plating gives a thin flash coating over the entire surface to ensure conductivity and proper current distribution. This minimizes burning, pitting, and other plating defects.
Brass Plating Chemistry and Operation
The primary brass plating tank contains the plating chemistry that deposits the desired brass finish when electrical current is applied. The basic constituents in a brass plating solution include:
- Copper metal ions (from copper cyanide or copper pyrophosphate)
- Zinc metal ions (from zinc cyanide, zinc sulfate, or other zinc salts)
- Complexing agents – Rochelle salts, phosphates, EDTA, etc.
- Conductive salts – sodium/potassium cyanide, pyrophosphates
- Buffering compounds to maintain pH
- Wetting agents and brighteners
By adjusting the ratio of copper to zinc ions, different brass alloy compositions can be deposited, ranging from 85/15 to 65/35 Cu/Zn. The plating bath is heated to 130-160°F to accelerate plating rates. Solutions should be periodically analyzed and replenished to maintain proper chemical balance.
During plating, the negatively-charged cathode workpieces attract the positively charged copper and zinc ions in solution to deposit the brass alloy coating. Specially-shaped anodes made of brass or copper and zinc alloy blocks complete the electrical circuit.
Current density typically ranges from 10-50 A/ft2 depending on the desired plating rate and properties. Higher current densities produce faster deposition but may reduce quality. Agitation is used to keep solution homogeneous and the cathode workpieces should be periodically reversed to even out the deposit thickness.
Rinsing After Plating
Once the desired plating thickness has been achieved, workpieces must be thoroughly rinsed again. Plating solutions contain contaminants that can stain and tarnish the plated surface if not completely removed.
Parts are withdrawn from the plating tank and immersed in a series of cold overflowing rinse tanks. A minimum 5-stage rinse is recommended, with the first tank agitated to accelerate rinsing. The final water conductivity should test below 20 μS/cm.
Proper rinsing prevents staining on the plated surface and also prevents dragout of plating chemistry back into rinse tanks. Following plating with sufficient rinsing provides clean parts ready for finishing steps.
Post-Plating Finishing and Inspection
After plating, additional finishing steps help make the plated layer more attractive and durable. The brass plating is enhanced with a clear top coat and then buffed and polished to a bright luster. Thorough inspection ensures quality plating.
Applying a Top Coat
For added tarnish and abrasion resistance, brass plated parts commonly receive a thin top coat of chromium or nickel. This helps the finish better withstand corrosion, weathering, and handling without dulling.
- Chromium – Parts are plated in a chromic acid solution containing chromate or sulfate ions. The thin layer of chromium oxide creates a transparent protective barrier over the brass.
- Nickel – Electroless or electrolytic nickel provides a smooth, hard nickel coating up to 0.0005 inches thick. This strengthens the finish and enhances reflectivity.
The top coat should be evenly applied and free of pits or thickness variations that could detract from appearance. It adds a level of durability while still allowing the underlying brass to show through.
Drying the Plated Parts
Before further finishing, plated parts must be completely dried to prevent water spots. Allowing parts to air dry at ambient temperature takes hours and risks oxidation starting. A better method is force drying in a hot air oven or using air blowers.
Parts are dried for 10-20 minutes at 150-200°F until all visible moisture is removed. Infrared drying can also quickly evaporate residual rinse water. Thorough drying prepares parts for reliable buffing, polishing and top coating.
Inspecting for Defects
After plating, rinsing, and drying, parts should undergo careful inspection to verify quality. The plating should completely cover all surfaces with a uniform brass deposit free of defects.
Typical plating defects to look for include:
- Pitting – Small holes and pores in plated layer due to impurities or additive depletion.
- Burning – Dark burnt areas caused by excess current density.
- Striations – Wavy plating thickness due to current fluctuations.
- Dull areas – Poor reflectivity due to surface contamination.
- Blisters – Bubbles of gas trapped between substrate and plating.
Any parts with inadequate plating coverage or other defects must be reworked to meet specifications. This may involve stripping and re-plating or touch-up plating flawed areas.
Buffing and Polishing
To maximize brightness and luster, brass plated parts undergo buffing and mechanical polishing. This removes any final microscopic roughness and really makes the finish pop.
Buffing is performed using rotating muslin or cotton wheels loaded with cutting compounds like fine rouge powder or aluminum oxide. The abrasive friction action smoothes the plating to a uniform satin sheen.
Final polishing uses softer buffing wheels and finer polishing pastes containing chromium or cerium oxide. This brings out a mirror-like shine. The brass finish takes on a brilliant golden color after buffing and polishing.
Applying a Clear Top Coat
For decorative brass components that will be handled frequently, a final clear acrylic or epoxy top coat can be sprayed or dipped over the polished plating. This adds scratch protection and prevents tarnishing of the finish over time.
The clear top coat seals the surface while still allowing the underlying polished brass to show through. It provides a durable maintenance-free finish that retains the freshly-buffed luster and avoids wear.
Key Factors That Affect Brass Plating Quality
Achieving high quality brass plating requires careful control of process variables. Here are some of the most important factors to monitor and optimize:
Surface Preparation
Thorough degreasing, pickling, activation and rinsing sets the stage for defect-free plating. Any oils, oxides or acids left on the surface will interfere with proper plating adhesion and coverage.
Solution Concentration
The plating bath contents must be maintained at the correct concentrations. Too low dilutes the solution, reducing plating speed and quality. Too high risks burning and brittle deposits. Regular analysis and additions are required.
Solution Filtration
Contaminants cause pitting and roughness. Continuous filtration removes particulates and organic impurities. Activated carbon filters adsorb organics.
pH Control
Precise pH control is crucial for optimal plating deposition. Each bath has a target pH range. If pH drifts too high or low, poor quality uneven plating results.
Temperature Management
Elevated temperatures accelerate plating speed but also affect deposit properties. Overheating the bath degrades additives while too cold slows plating.
Anode Maintenance
Dirty or passive anodes increase resistance and disrupt the plating current flow. Anodes must be cleaned and replaced routinely to support optimal plating.
Part Fixturing
Proper racks, hooks and wiring ensure parts are immersed correctly and current distributes evenly throughout the rack. Poor fixturing causes plating variations.
Agitation
Keeping solutions mixed and moving helps replenish plating ions and prevents buildup of gases. Stagnant areas lead to defects. Moderate agitation is best.
By mastering these key parameters and fine-tuning the details, brass plating can be performed reliably and repeatably for high quality results. Consistency is key for large production runs.
Brass vs Other Plating Options
Brass plating has distinct advantages that make it preferable over other plating technologies for certain applications:
Appearance – Brass has an attractive golden color perfect for decorative finishes. Its soft golden sheen is warmer and more subtle than the brassy glare of chrome.
Solderability – Brass coated parts can be readily soldered. Many other plating finishes like nickel and chrome cannot be soldered.
Wear Resistance – Brass provides better wear protection than copper, tin, and silver plating. It holds up to friction and abrasion.
Corrosion Resistance – Brass naturally resists tarnish, corrosion, and weathering better than copper or steel. It performs well outdoors.
Cost – Brass plating is less expensive compared to gold or rhodium plating. It provides good value for the performance.
Versatility – Brass plates evenly over all common metals. Parts with multi-metal construction can be brass plated.
Ease of Repair – Brass finishes can be easily stripped and re-plated if repair is needed. Other plating can be difficult to remove.
For applications requiring an attractive gold-toned finish, good wear properties, and the ability to solder, brass plating is an optimal choice.
Brass Plating Applications
Here are some of the most common industrial and decorative uses for brass electroplating:
- Plumbing fixtures – Faucets, valves, pipe fittings
- Electrical hardware – Outlets, switches, lamp parts
- Automotive trim – Grilles, emblems, wheel accents
- Marine components – Cleats, rails, propellers
- Musical instruments – Trumpets, trombones, saxophones
- Jewelry findings – Chains, charms, settings
- Furniture hardware – Hinges, pulls, knobs, fasteners
- Door accessories – Knockers, kick plates, push bars
- Bathroom accessories – Towel bars, robe hooks, shower caddies
Brass plating creates a finished look or enhances appearance and functionality. The plating can match genuine solid brass components or provide brass styling on less costly base metals.
Key Takeaways on Brass Plating
- Brass electroplating involves submerging parts in a plating bath containing copper and zinc ions and depositing a brass alloy coating via electrical current.
- Thorough surface preparation like degreasing, pickling, and activation ensures flawless plating adhesion and coverage.
- Strike plating with copper or nickel provides an initial conductive layer for subsequent brass deposition.
- Precise control of solution chemistry, temperature, current density and other parameters is crucial for high quality plating.
- Finishing steps like adding a clear top coat, buffing, and polishing maximize the aesthetic appearance and durability of the plated brass.
- Compared to other plating methods, brass offers attractive warm coloration, good wear properties, solderability, and corrosion resistance.
- Brass plating has widespread usage across plumbing, electrical, automotive, marine, and decorative applications.